Tech
Understanding PCB&PCBA Manufacturing: A Complete Guide
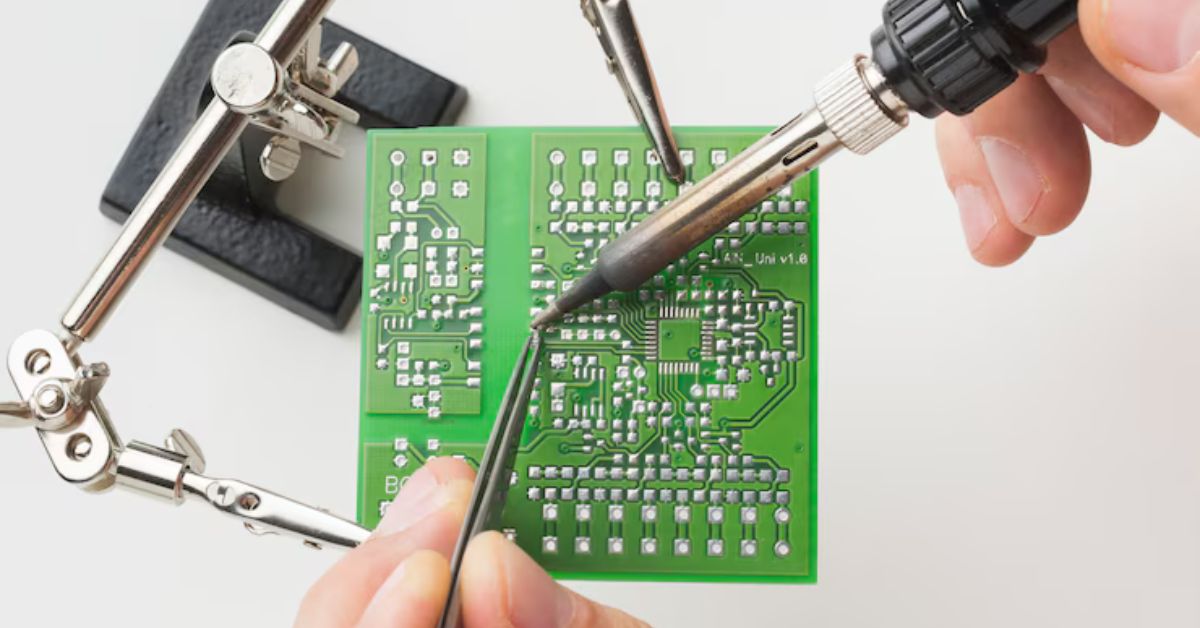
In the world of modern electronics, PCB&PCBA manufacturing plays a central role in shaping everything from smartphones and medical devices to industrial machines and automobiles. Printed Circuit Boards (PCBs) and Printed Circuit Board Assemblies (PCBAs) are the backbone of virtually all electronic devices, making their design and manufacturing processes essential to ensuring product performance, reliability, and innovation.
This article explores the intricate details of PCB&PCBA manufacturing, the technologies involved, common challenges, and the industry’s future.
What is PCB and PCBA?
A PCB (Printed Circuit Board) is a flat board that connects electronic components using conductive tracks, pads, and other features etched from copper sheets and laminated onto a non-conductive substrate. PCBs serve as the physical platform for mounting and interconnecting electronic components in a compact and reliable manner.
PCBA (Printed Circuit Board Assembly), on the other hand, refers to the process of mounting electronic components onto the PCB to make it a fully functioning electronic assembly. The PCBA includes resistors, capacitors, ICs (integrated circuits), and other surface-mount or through-hole components.
The Evolution of PCB&PCBA Manufacturing
The origins of PCB manufacturing date back to the early 20th century, but it wasn’t until the mid-20th century that PCBs began to see widespread adoption in consumer and industrial electronics. As technology advanced, the size of electronic devices shrank, requiring more compact and efficient PCBs. This evolution led to the development of multilayer PCBs and more advanced PCBA techniques, enabling the modern PCBA manufacturer to integrate more functionality into smaller spaces with greater precision and reliability.
Today, PCB&PCBA manufacturing has evolved into a high-precision, highly automated industry. With the growth of sectors such as automotive electronics, IoT (Internet of Things), and 5G technology, the demand for high-performance PCBAs continues to rise.
PCB Manufacturing Process
The manufacturing of a PCB begins long before any electronic components are placed on it. It starts with the design, usually created using CAD software, which is then used to create photomasks for each layer of the board.
The substrate material, commonly made of fiberglass-reinforced epoxy laminate (FR4), is coated with a layer of copper. This copper is then etched away to form the conductive pathways based on the design layout. The process includes drilling holes (vias), plating through-holes, and applying solder mask and silkscreen layers.
Solder masks are applied to protect copper traces from oxidation and to prevent solder bridges during the PCBA process. The silkscreen layer is printed on the board to indicate component locations, logos, or other important information.
Advanced PCBs may include multiple layers, which are laminated together using heat and pressure. The precision in layering and alignment is crucial to the board’s performance and integrity.
PCBA Manufacturing Process
Once the PCB is manufactured, it moves on to the PCBA stage. This involves placing and soldering the components onto the board. The two main methods used in PCBA are Surface Mount Technology (SMT) and Through-Hole Technology (THT).
In Surface Mount Technology, components are mounted directly onto the surface of the PCB using solder paste. The board is passed through a reflow oven, where the paste melts and forms reliable electrical connections.
Through-Hole Technology, although less common in modern high-density assemblies, is still used for components requiring greater mechanical strength. Holes are drilled through the board, and component leads are inserted and soldered, typically using wave soldering.
Automated optical inspection (AOI), X-ray inspection, and functional testing ensure the board is free from defects. The completed PCBA is then cleaned to remove any residual flux or contaminants before being integrated into final products.
Importance of Quality Control in PCB&PCBA Manufacturing
Quality control is critical in PCB&PCBA manufacturing to ensure product reliability and compliance with industry standards. The smallest defect can cause malfunctions or safety issues, especially in medical or automotive applications.
Manufacturers perform rigorous inspections at every stage of the process. In PCB manufacturing, this includes checking the alignment of layers, copper trace integrity, and hole accuracy. In PCBA, inspections focus on component placement, soldering quality, and electrical connectivity.
Advanced techniques such as flying probe testing, in-circuit testing, and burn-in testing are used to verify the board’s performance under real-world conditions. Consistent quality control helps reduce rework, increase yield, and maintain customer trust.
Materials Used in PCB&PCBA Manufacturing
The choice of materials in PCB&PCBA manufacturing significantly influences the performance, durability, and cost of the final product. Common substrate materials include FR4, polyimide, and PTFE, each offering specific benefits such as heat resistance or flexibility.
Copper is the most widely used conductor due to its excellent electrical conductivity. For high-frequency applications, materials with low dielectric constants and loss tangents are used to ensure signal integrity.
Solder pastes and fluxes used in PCBA must be compatible with both the components and the board to ensure proper bonding and long-term stability. The choice of components also depends on the intended application, operating environment, and regulatory requirements.
Challenges in PCB&PCBA Manufacturing
Despite technological advancements, manufacturers face numerous challenges in PCB&PCBA production. One major challenge is miniaturization. As electronic devices become smaller, the boards must accommodate more components in a compact space without sacrificing performance or reliability.
Thermal management is another concern. High-speed and high-power devices generate significant heat, which must be effectively dissipated to avoid damage. Manufacturers employ heat sinks, thermal vias, and specialized materials to address this issue.
Supply chain complexity can also impact the availability of components, especially during global disruptions. Ensuring a steady supply of high-quality parts is vital for maintaining production schedules.
Environmental compliance with regulations such as RoHS (Restriction of Hazardous Substances) and REACH (Registration, Evaluation, Authorisation and Restriction of Chemicals) adds further complexity to material selection and process control.
Technological Innovations in PCB&PCBA Manufacturing
The field of PCB&PCBA manufacturing has seen continuous innovation, driven by the need for higher performance, better efficiency, and reduced environmental impact. High-Density Interconnect (HDI) PCBs allow more components and connections within a smaller area, which is essential for smartphones, wearables, and other compact devices.
Flexible and rigid-flex PCBs have enabled new design possibilities, particularly in medical and aerospace applications where space constraints and movement require adaptable solutions.
Automated assembly with advanced robotics and machine learning has improved accuracy, reduced human error, and accelerated production. Real-time monitoring systems provide immediate feedback, allowing manufacturers to make quick adjustments.
3D printing and additive manufacturing techniques are beginning to influence PCB prototyping, reducing time-to-market and allowing for rapid design iterations.
Applications of PCB&PCBA Across Industries
Virtually every industry that uses electronics relies on PCB&PCBA manufacturing. In consumer electronics, they form the core of smartphones, tablets, and laptops. The automotive industry uses advanced PCBAs in engine control units, infotainment systems, and electric vehicle power systems.
In medical technology, PCBs are essential in imaging systems, diagnostic tools, and wearable health monitors. These applications require high reliability and often must meet stringent safety standards.
Aerospace and defense demand rugged and high-performance PCBAs capable of operating under extreme conditions. These boards must pass rigorous testing to ensure they can withstand temperature fluctuations, vibrations, and radiation.
Industrial automation, including robotics and control systems, depends on PCBAs for precision and consistency in operations. Even emerging sectors like smart agriculture and renewable energy utilize custom-designed PCBAs to optimize performance.
Environmental Impact and Sustainability
With the increase in electronic waste and the need for sustainable practices, the PCB&PCBA manufacturing industry is taking steps to reduce its environmental footprint. Manufacturers are investing in lead-free soldering processes, recyclable materials, and energy-efficient production techniques.
Efforts are also being made to design PCBs for easy disassembly and recycling, allowing valuable metals and components to be recovered at the end of a product’s lifecycle.
Some companies are exploring the use of biodegradable substrates and green laminates to further minimize environmental impact. Regulatory bodies and environmental organizations continue to influence the direction of sustainable manufacturing practices.
The Future of PCB&PCBA Manufacturing
The future of PCB&PCBA manufacturing is promising, with exciting developments on the horizon. The rise of smart electronics, IoT, 5G, and AI-integrated systems is pushing manufacturers to innovate faster and deliver highly complex, compact, and high-performance PCBAs.
Digital twins, augmented reality in design and assembly, and predictive maintenance through AI and IoT are likely to transform the industry further. These technologies will enhance manufacturing efficiency, reduce errors, and improve product quality.
Moreover, the demand for custom PCBs is increasing, especially in niche markets like wearable technology, drones, and personalized medical devices. Companies offering quick-turn prototyping and end-to-end design-to-manufacturing services are gaining an edge in this competitive space.
Conclusion
PCB&PCBA manufacturing is the backbone of modern electronics, supporting innovation across industries. From the initial design and substrate preparation to final component assembly and inspection, the process is a complex blend of precision engineering, material science, and automation.
As the world becomes more connected and reliant on smart technology, the demand for advanced PCBAs will only grow. Manufacturers who invest in quality, sustainability, and technological innovation will be best positioned to meet the challenges and opportunities of the future.
Whether you’re a startup designing your first electronic product or a global enterprise scaling complex systems, understanding the dynamics of PCB&PCBA manufacturing is key to achieving success in today’s high-tech landscape.