Tech
Non-Destructive Testing Methods in API 653 Inspections
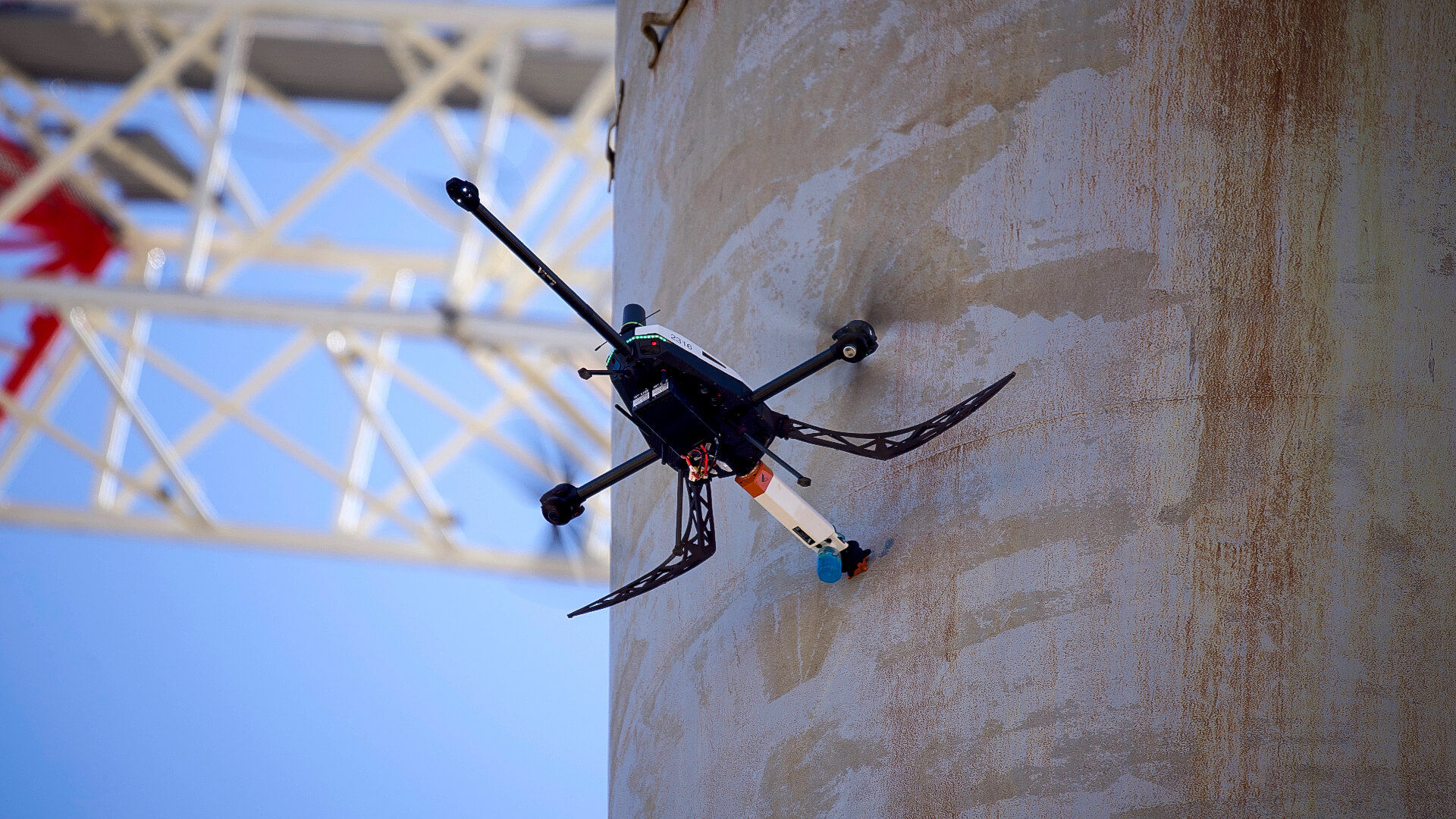
When it comes to aboveground storage tanks, prevention is always better than a costly disaster. That’s where API 653 inspection comes in, ensuring that tanks are structurally sound, compliant with industry regulations, and safe for continued operation. But how do inspectors evaluate the integrity of a tank without causing damage? The answer lies in non-destructive testing (NDT) methods.
NDT techniques allow inspectors to assess tank conditions without cutting, breaking, or permanently altering the structure. This approach not only saves time and money but also minimizes downtime and prevents unnecessary risks. Let’s dive into the key NDT methods used in API 653 inspections and how they help ensure tank safety and compliance.
1. Ultrasonic Testing (UT) for Thickness Measurements
Ultrasonic testing is one of the most commonly used NDT methods in API 653 inspections. It relies on high-frequency sound waves to measure the thickness of a tank’s walls and bottom plates. By sending sound waves through the material and analyzing the echoes, inspectors can detect corrosion, erosion, and material loss.
Why it matters: Even a small reduction in thickness can compromise a tank’s structural integrity. UT helps identify thinning areas early, allowing for preventative maintenance before a failure occurs.
2. Magnetic Particle Testing (MT) for Crack Detection
Magnetic particle testing is used to detect surface and near-surface cracks in ferromagnetic materials like steel. During this process, a magnetic field is applied to the tank’s surface, and fine iron particles are spread across it. If there are any cracks, they create magnetic field distortions that attract the particles, making flaws easily visible.
Why it matters: Even microscopic cracks can expand over time, leading to costly leaks or catastrophic failures. MT helps identify these flaws before they escalate.
3. Dye Penetrant Testing (PT) for Surface Defects
Dye penetrant testing is another widely used method for detecting surface defects, particularly in non-magnetic materials. A special dye is applied to the surface, allowed to seep into cracks, and then wiped clean. A developer is then sprayed over the area, drawing out the dye from the cracks and making imperfections visible under UV or white light.
Why it matters: PT is effective for identifying hairline cracks, weld defects, and other surface flaws that might be missed by visual inspection alone.
4. Radiographic Testing (RT) for Internal Defects
Radiographic testing uses X-rays or gamma rays to penetrate a tank’s structure and create an image of its internal components. This method allows inspectors to detect hidden defects, such as voids, inclusions, or weld imperfections.
Why it matters: RT is highly effective for evaluating weld quality and detecting internal defects that other methods may not reveal. It’s crucial for ensuring the long-term reliability of a storage tank.
5. Acoustic Emission Testing (AET) for Real-Time Monitoring
Acoustic emission testing is a unique NDT method used by tank inspection company that detects stress waves generated by active cracks or material degradation. Sensors are placed on the tank, and when structural changes occur, they emit sound waves that are recorded and analyzed.
Why it matters: AET provides real-time data on structural integrity, making it useful for monitoring tanks under operational conditions and detecting early signs of failure.
6. Visual Inspection (VT) as the First Line of Defense
While advanced NDT techniques play a crucial role, visual inspection remains the first step in an API 653 assessment. Inspectors look for visible signs of corrosion, leaks, deformation, or coating degradation.
Why it matters: A trained inspector can often spot early warning signs that indicate the need for more in-depth testing. VT is cost-effective and essential for any inspection process.
7. Leak Testing (LT) for Identifying Tank Weaknesses
Leak testing involves applying pressure or a tracer gas to a tank to detect any escape points. Techniques like bubble testing, vacuum box testing, and tracer gas detection help pinpoint leaks that may not be visible.
Why it matters: Even small leaks can lead to significant environmental and financial consequences. LT helps ensure tanks are sealed and functioning properly.
Why NDT Matters in API 653 Inspections
Non-destructive testing is an integral part of API 653 inspections because it provides accurate data without compromising tank integrity. These methods allow inspectors to:
- Detect early-stage defects before they become critical failures
- Minimize downtime by avoiding invasive procedures
- Extend the lifespan of storage tanks through preventative maintenance
- Ensure compliance with safety and environmental regulations
Regular API 653 inspections incorporating NDT methods are essential for industries relying on aboveground storage tanks, including oil and gas, chemicals, and water storage. By investing in these inspections, companies can reduce risks, prevent costly repairs, and maintain safe operations.
Final Thoughts
Non-destructive testing is the backbone of API 653 inspections, offering a precise, cost-effective, and reliable way to assess tank conditions. Whether it’s ultrasonic testing for wall thickness, magnetic particle testing for cracks, or radiographic testing for internal flaws, each method plays a critical role in maintaining tank safety and compliance.
For businesses operating storage tanks, regular inspections using NDT techniques aren’t just a regulatory requirement—they’re a proactive strategy to protect assets, reduce liabilities, and ensure long-term operational success. By staying ahead of potential failures, companies can keep their tanks—and their bottom line—secure for years to come.